Cómo analizar la capacidad de producción de la empresa.
Si partimos de la premisa que ‘el cambio es lo único que permanece’, podremos concluir que la manera de hacer las cosas en las empresas, no pasa desapercibida, esto obliga a tener una nueva visión de hacerlas al interior. Sobre todo el cambio en los mercados y la tecnología, que son altamente influyentes en los procesos productivos empresariales, he ahí la necesidad de analizar la capacidad de producción de la empresa.
Con los cambios ocurridos en los últimos años en los mercados y la tecnología, podemos vislumbrar algunos más drásticos que hicieron que la manera de enfrentar el trabajo al interior de las empresas en lo productivo fuera diferente, a continuación podremos observar aspectos que cambiaron en los mercados y que ‘hoy’ nos hacen enfrentarnos a algunos muy diferentes a los de ‘ayer’:
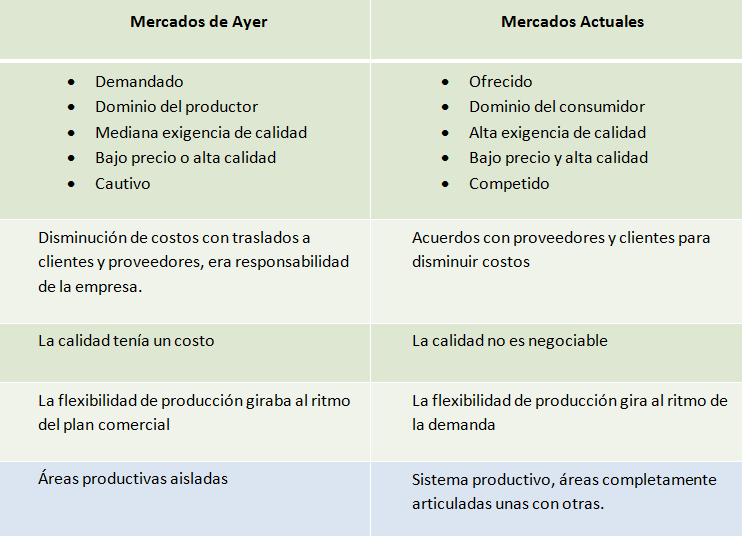
Hoy en día la apertura de fronteras y mercados, el crecimiento de la competencia a nivel mundial, las exigencias crecientes de los consumidores (calidad del servicio y producto), el incremento de opciones de productos con alto valor agregado, la forma de su presentación, la especialización en su aprovisionamiento, distribución y transporte, la tecnología, entre otras razones, obligan a las organizaciones a encontrar mejores y más ágiles maneras de manejar el flujo físico de la materia prima, componentes, materiales, producto final y flujo de información, desde la fuente del proveedor, pasando por el proceso de fabricación, hasta la entrega del producto al consumidor, todo esto debe ir acompañado de un excelente servicio, el cual al final es lo que posiciona la empresa frente al consumidor final (satisfacción del cliente).
Cuando nos referimos a “satisfacción del cliente” queremos decir que: el cliente solo queda satisfecho cuando le entregamos el producto en óptimas condiciones de calidad, a un precio competitivo, en el tiempo que él lo necesita y en el lugar convenido.
Todos estos elementos dependen de todas las áreas de la organización y el cual nos lleva a pensar en un sistema productivo empresarial y del cual dependerá la competitividad de la empresa en el futuro.
Por todo lo anterior, hoy las empresas no se preparan para producir y luego vender, sino para producir lo que les están demandando. Así pues, su capacidad de producción debe adaptarse a esa condición de satisfacer las necesidades del cliente y las de su empresa, a fin de no sufrir con los excedentes.
Hoy no existen empresas más grandes, ni mas rápidas, pero si más inteligentes que otras.
Las empresas Inteligentes son las que poseen la suficiente información de los procesos para tener el poder de manipularlos de acuerdo a las condiciones de mercado mencionadas anteriormente.
Cuando estamos en una empresa y conocemos: Cuántos trabajadores hay en su empresa, cuántos de ellos están en la línea de producción directa de productos o de órdenes de trabajo, cuántos en puestos administrativos, de ventas, mantenimiento u otras funciones, cuántas unidades de producto produce la empresa en una jornada normal, o en su caso, cuántas órdenes atienden o despachan al día, si todos realmente producen una parte del proceso o de la orden de un cliente, cuántos trabajadores son necesarios para atender la carga de pedidos de un día normal, entre otros. No es suficiente, a menos que éstas provengan de un mapa de operaciones de la empresa, y que nos muestre todos los diagramas de flujo de los procesos y sus actividades al detalle; el cual se debe calcular de acuerdo a las necesidades.
Toda compañía debe tener su mapa de procesos formalizado, documentado, sistematizado, controlado (mejoramiento continuo) e implementado. En caso contrario, la compañía puede estar a la “deriva”.
Así pues, la capacidad real de producción de una empresa, será determinada por la capacidad real de los distintos procesos que ejecutan las empresas y sus tiempos.
Antes de mencionar el método para calcular la capacidad es conveniente mencionar que por todo lo expuesto anteriormente, digamos, que las características de los procesos deben ser flexibles, ágiles, sencillos, fáciles, a fin de poderse adaptar a nuevas condiciones de mercado y tecnología.
ANTES
- Trabajaba para el pasado
- Toleraba el rechazo
- Buscaba cumplir con las especificaciones
- Se comprometía con el producto
- Si algo estaba mal se detectaba al final del proceso.
AHORA
- Trabaja para el futuro
- Evita el rechazo
- Busca el mejoramiento permanente
- Se compromete con el proceso
- Si algo está mal, se detecta en la misma área
Un método práctico que se recomienda para calcular la capacidad de producción es el siguiente:
1) Obtener el mapa completo de las operaciones productivas normalizadas al detalle.
2) Medir los tiempos de cada actividad del proceso (10 mediciones por lo menos, en diferentes momentos del día y turnos y a diferentes trabajadores), para al final sacar un tiempo promedio que sea representativo. A este tiempo se le llama Tiempo Normal (TN).
Tiempo normal (TN) = t1+t2+t3+t4+t5+t6+t7+t8+t9+t10 / 10
3) Teniendo en cuenta que una jornada de trabajo tiene 8 horas; pero sabemos que las personas no podemos mantener un trabajo totalmente continuo en períodos largos de tiempo (relativos a la jornada). Es decir: de las 8 horas disponibles, no podemos esperar que se producirá todo el tiempo. Se acumulan pequeños momentos de no producción. A ese tiempo no efectivo en trabajo, se denomina “Tiempo no efectivo o de Tolerancia” o, también lo conocemos como: grado de eficiencia de la mano de obra; normalmente es representado con un porcentaje. Por estudios realizados, se conoce que, con normalidad, en grupos bien dirigidos ésta eficiencia alcanza un 85%; es decir las personas hacen trabajo efectivo solo el 85% de su jornada de 8 horas. De tal forma que 80 minutos del día son, muy normalmente, gastados en cosas como: estirarse un poco, alguna conversación con compañeros, ir al baño, tomar agua, arreglar cosas, baja por cansancio, etc. Al tiempo resultado que tiene en cuenta lo anterior (Tolerancias) se le llama Tiempo Normal Estándar. De tal forma que:
Tiempo Normal Estándar (TNE)= (8 x 60 / TN) x 0.85 (capacidad máxima de producción en 8 horas de trabajo)
4) Con este dato, ya sabemos cuanta es la máxima producción que esperaríamos de este proceso si todo transcurriera con normalidad y sin tropiezos adicionales; pero se sabe que no existe un proceso sin tropiezos ni alteraciones de diversa índole, que ocurren y que no tienen que ver con el rendimiento propio del personal, sino que se deben a otros factores. Esos inconvenientes productivos también tienen su impacto directo en alterar la capacidad de diseño y deben ser considerados al establecer nuestra capacidad real de producción. Donde el número 0.88 es un factor de merma inherente al proceso conveniente para tener en cuenta en el cálculo, en la Capacidad real de produccion,de tal forma que :
TNE x 0.88= Capacidad real de producción.
5) Este valor debe ser considerado como nuestra capacidad real de producción y con relación a él debe medirse diariamente el rendimiento obtenido en las jornadas de 8 horas. El cálculo realizado nos marca cuál es el nivel que tomaremos como nuestro 100% de eficiencia.